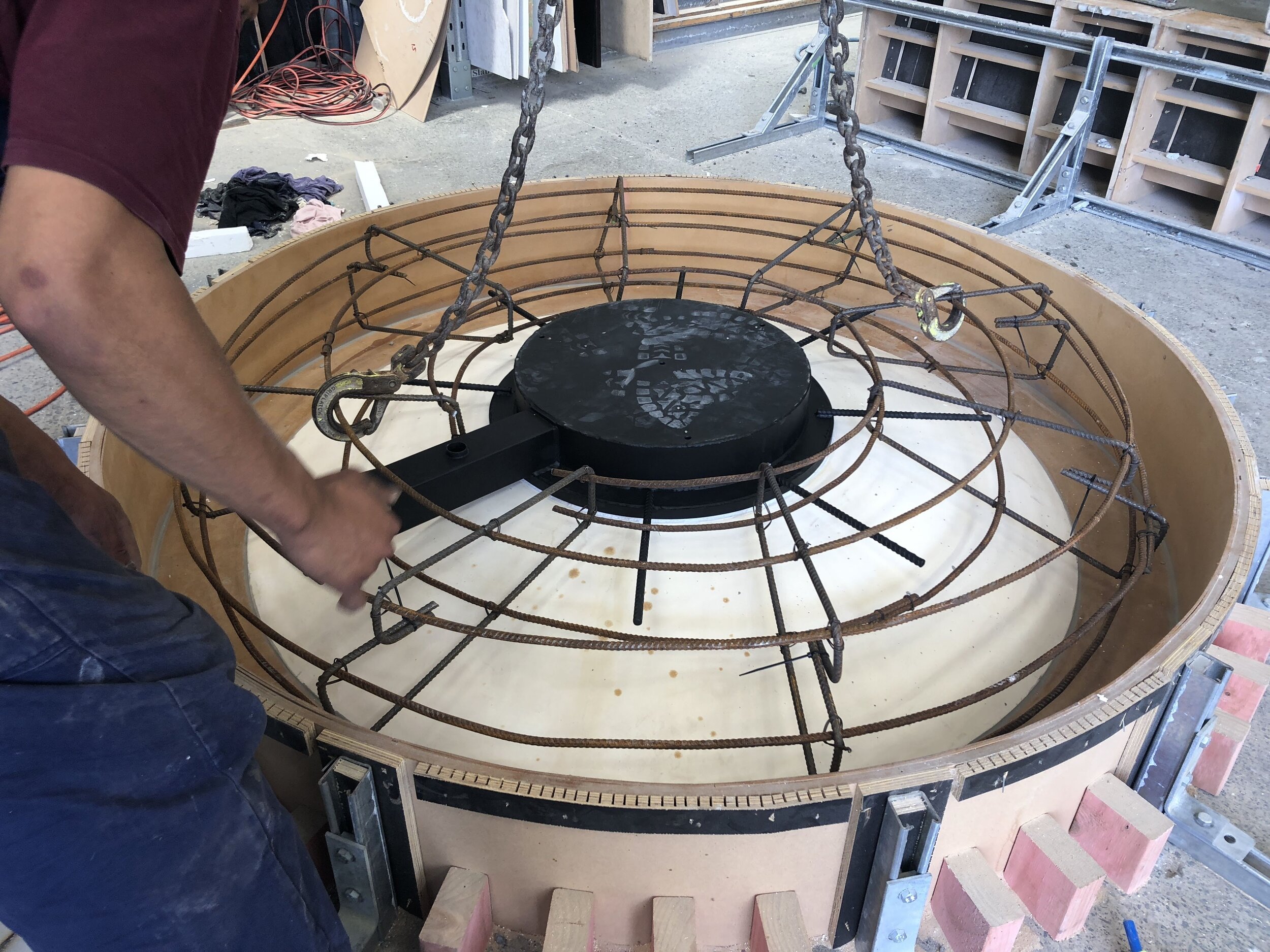
Design and Fixing of GRC cladding for Architects & Engineers
At Liquidstone, we craft high-performance Glass Fibre Reinforced Concrete (GRC, also known as GFRC) cladding panels and rainscreens for commercial buildings. GRC offers a superior alternative cladding materials, providing unparalleled design flexibility, cost efficiencies, faster project delivery, and a lower embodied carbon footprint when compared to traditional concrete. This guide is designed to empower Architects and Engineers to harness the full potential of GFRC in their next project.
The Power of GFRC: Benefits for Your Designs
GFRC is a composite material made from hydraulic cement, silica sand, alkali-resistant (AR) glass fibres, and water. The inclusion of glass fibres significantly enhances the mortar mix, improving its tensile and flexural characteristics.
Key Advantages of GFRC:
Lightweight & Strong: GFRC panels offer substantial weight savings compared to traditional precast concrete alternatives. This translates to significant cost reductions in transportation, handling, and erection, and can lead to substantial economies in the design of foundations and superstructures for high-rise buildings.
Design Flexibility: GFRC can be moulded into a wide variety of complex shapes and profiles, making it ideally suited for modern building exteriors that utilize lightweight, prefabricated cladding panels. This includes the creation of intricate 3-dimensional forms, curves, and diverse textures and patterns.
Durability & Performance: GFRC boasts excellent durability, chemical resistance, non-combustibility, and good sound/heat insulation properties6. It also exhibits impact resistance.
Sustainability: By significantly reducing weight, GFRC contributes to lower embodied carbon in construction compared to heavier concrete solutions.
Cost & Program Benefits: The lightweight nature and ease of prefabrication lead to lower overall project costs and faster installation times
GRC Panel Types
Liquidstone manufactures a range of GFRC cladding panels designed to meet diverse architectural and engineering requirements.
Our Standard Panel Types Include:
Curved or Flat Panels: These versatile panels can be produced in various configurations, offering significant design freedom.
Horizontal Inter-floor Spandrel Panels: Ideal for concealing floor edges and structural elements between floors.
Vertical Column Cladding Panels: Perfect for enhancing the aesthetic and protective qualities of structural columns.
Horizontal Spandrel Panels at Roof Level: Used for architectural finishing and protection at the top of a building.
The most common types of GRC construction are stud frame construction and ribbed panel construction. While flat, rectangular GRC pieces are used for very small areas like roof tiles, larger cladding panels require ribs or corrugations for strengthening and stiffening to resist wind and seismic forces.
Standard GRC Flat Panel sizes
Horizontal spandrel and column type panels
Size parameters
Common GFRC Panel Constructions:
Ribbed Panel Construction: This involves flat panels strengthened and stiffened by ribs or corrugations, typically along all external edges and internally.
Stud Frame Construction: This popular method consists of a single GRC skin attached to a prefabricated frame (usually metal) using flexible and gravity anchors. This system allows for the manufacture, transportation, and erection of very large, often flat, panels (e.g., 10−20m2). Stud frame construction is particularly suitable for resisting earthquake damage.
GFRC Fixing Methods for Optimal Performance
Proper fixing methods are crucial for the long-term performance and aesthetic integrity of GFRC cladding. They must secure panels, accommodate movement, allow for construction inaccuracies, and maintain integrity under various conditions like impact, vibration, wind, and fire. It's essential to avoid "over-fixing" GRC panels, as this can inhibit natural movements and lead to detrimental cracking.
Common Fixing Methods:
Face Fix / Direct fix: Used where access is restricted or panels are small, with the fixings visible on the panel's face. Face fixings at the base of the panel provide vertical support through their shear resistance, while all fixings provide lateral support.
Bracket Fix: This method typically involves stainless steel cast-in sockets anchored into the GRC panel, spreading the load over a larger area. These sockets should be encapsulated in an adequate volume of GRC with good fibre distribution and left slightly proud of the GRC surface to prevent damage from overtightening.
GFRC Panels with Steel Sub-frame Support: This advanced method involves attaching the GFRC skin to a prefabricated metal frame. This is commonly used for large panels and is the preferred method for constructing back-ventilated and drained rainscreens.
Key Components of Sub-frame Support:
Flex Anchors: L-shaped flexible anchors provide lateral support to the GRC facing while allowing for rotation and shrinkage/moisture movement.
Gravity Anchors: Positioned along the bottom of the panels, these anchors support the self-weight of the GRC. They also stabilize the construction against wind action in service conditions. All gravity and flex anchors should point towards the center of the panel to alleviate adverse shrinkage stresses and should be fitted with debonding sleeves.
Threaded Inserts: Inserts are threaded connectors cast into GRC panels or structures during manufacturing. They help attach other parts to the GRC panels.
Mechanical Anchors for Veneers: For unbonded veneer facings like brick or natural stone fixed to the GRC surface, mechanical anchors connect them while allowing movement between veneer and GRC caused by temperature and moisture changes. These stainless steel anchors are set into the GRC and made to permit this movement. A bond breaker is usually placed between the veneer and GRC backing when using these anchors.
Typical stud frame
Example flex anchor
Example gravity anchor
Important Design Considerations for Fixings:
Movement Accommodation: Fixings must allow for translational and rotational movements between panels and the supporting structure, while maintaining waterproofing at joints. GRC is susceptible to dimensional changes due to wetting and drying, as well as thermal movements. These movements must not be inhibited.
Tolerances: Adequate tolerances must be incorporated into the fixing system to accommodate normal construction inaccuracies and anticipated movements.
Material Selection & Durability: Stainless steel fixings are generally recommended due to their high corrosion resistance and long life, especially in inaccessible locations or corrosive environments. Galvanised fixings have a finite life proportional to the zinc coating thickness.
Galvanic Corrosion Prevention: When dissimilar metals are in contact, galvanic corrosion can occur. This can be prevented by excluding water or isolating the metals with non-conductive materials like plastic or rubber gaskets and nylon/Teflon washers.
Lifting and Handling Fixings: Separate fixings should always be provided for lifting and handling purposes to avoid damaging permanent fixings. Lifting points should be symmetrically placed about the panel's center of gravity.
Early Design Coordination is Key
To ensure a safe, efficient, and economic fixing system, early design coordination between the Architect, Structural Engineer, and GRC Cladding Designer is paramount. Involving glazing/curtain walling specialists in these discussions is also advisable to address interface issues
What is GRC?
Constituent materials
Glass Fibre reinforced concrete (GRC) is a composite material made up of various constituent materials including; Binders (cement, pozzolans), Aggregates (silica sands), Fibre (Alkali resistant glass fibre), Admixtures (e.g. plasticisers, polymers, titanium dioxide, oxides etc) and water.
production
GRC is typically made in one of two methods, either ‘spray-up’ or ‘premix’. The method selected is largely dependant on the product being made (e.g. large flat panels vs complex 3D forms respectively) with each having their own advantages for the desired performance characteristics. With premix the fibre is pre-cut, mixed with the other ingredients and then hand pressed or trowelled into a mould. With the continuous spray method a glass fibre ‘roving’ is fed into a compressed air spray gun, where the fibres are cut to length and mixed simultaneously with a sand/cement slurry. Both methods require careful hand compaction into the mould using a spring roller.
For both methods Liquidstone first lay down a fine ‘mist’ coat which has no fibre onto the mould and this forms the decorative or face layer. Using this technique achieves a superior quality finish and often times means no additional post-production is required e.g. repairs, fairing, filling, painting etc.
Moulds and formwork
Moulds can typically be made from a variety of materials such as MDF, Plywood, Steel, Fibreglass and Polyurethane rubber etc or a combination of one or all of these materials.
Careful consideration must be taken to select the most appropriate material or combination of materials for each mould or application e.g. a single use one-off product will likely have a mould made using low cost material such as MDF whereas a mass produced product may benefit from a more expensive mould made from fibreglass with a PUR rubber liner that can be used many 100’s of times.
Surface finishes and treatments
There are almost limitless possibilities for colour and texture that can be applied post-production
Off-form - smooth or textured surfaces, intricate patterns
Exposed / fine aggregate including ‘Graphic concrete’ and Sand-blasting
Mechanical abrasion - honing / polishing
Painting / Staining - a wide range of colours and effects are achievable
Hydrophobic coating and sealers
Properties of GRC
Acoustic performance
Well designed GRC can be effectively used as sound attenuating barriers alongside motorways and railways lines etc. For example a 10mm thick GRC panel will provide 20kg of mass per square meter which when combined with relief patterns and perforations designed to diffract sound the GRC panel will provide excellent sound / acoustic barriers.
Permeability, water absorption and apparent porosity
Well compacted GRC has inherently low water permeability and can be used as for drains, culverts, pits and water tanks.
Fire resistance
The basic constituents of GRC are inorganic and non-combustible. The fire performance classification according to standard test procedure is “A1”.
Toughness and impact resistance
GRC is inherently tougher and more impact resistant than standard concrete and many other fibre reinforced composites.
Recycling of GRC
GRC products are suitable for recycling in a similar way to standard concrete and in fact due to the relative high percentage of cement can contribute to the development of additional strength in concrete made from recycled aggregates.
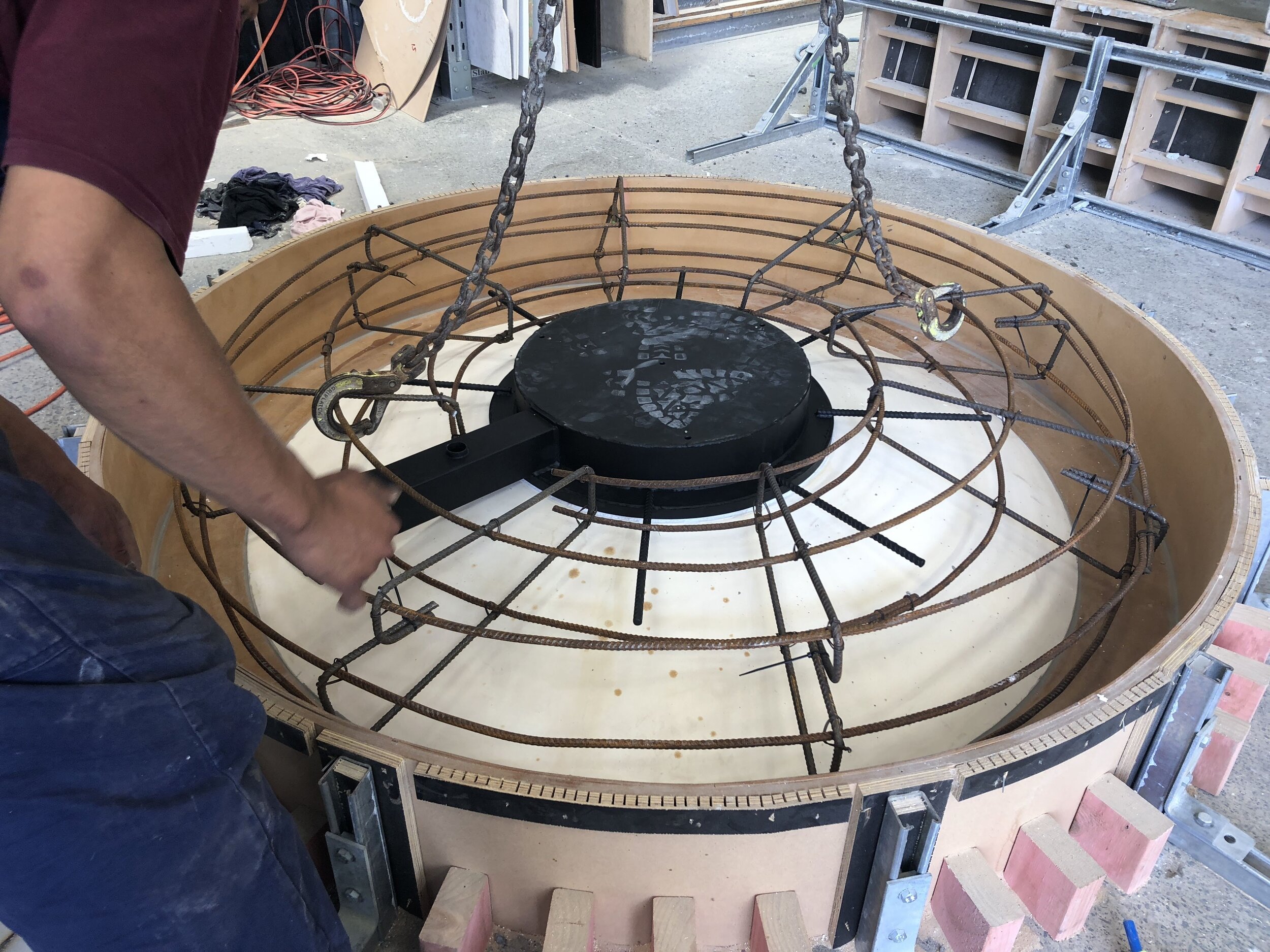
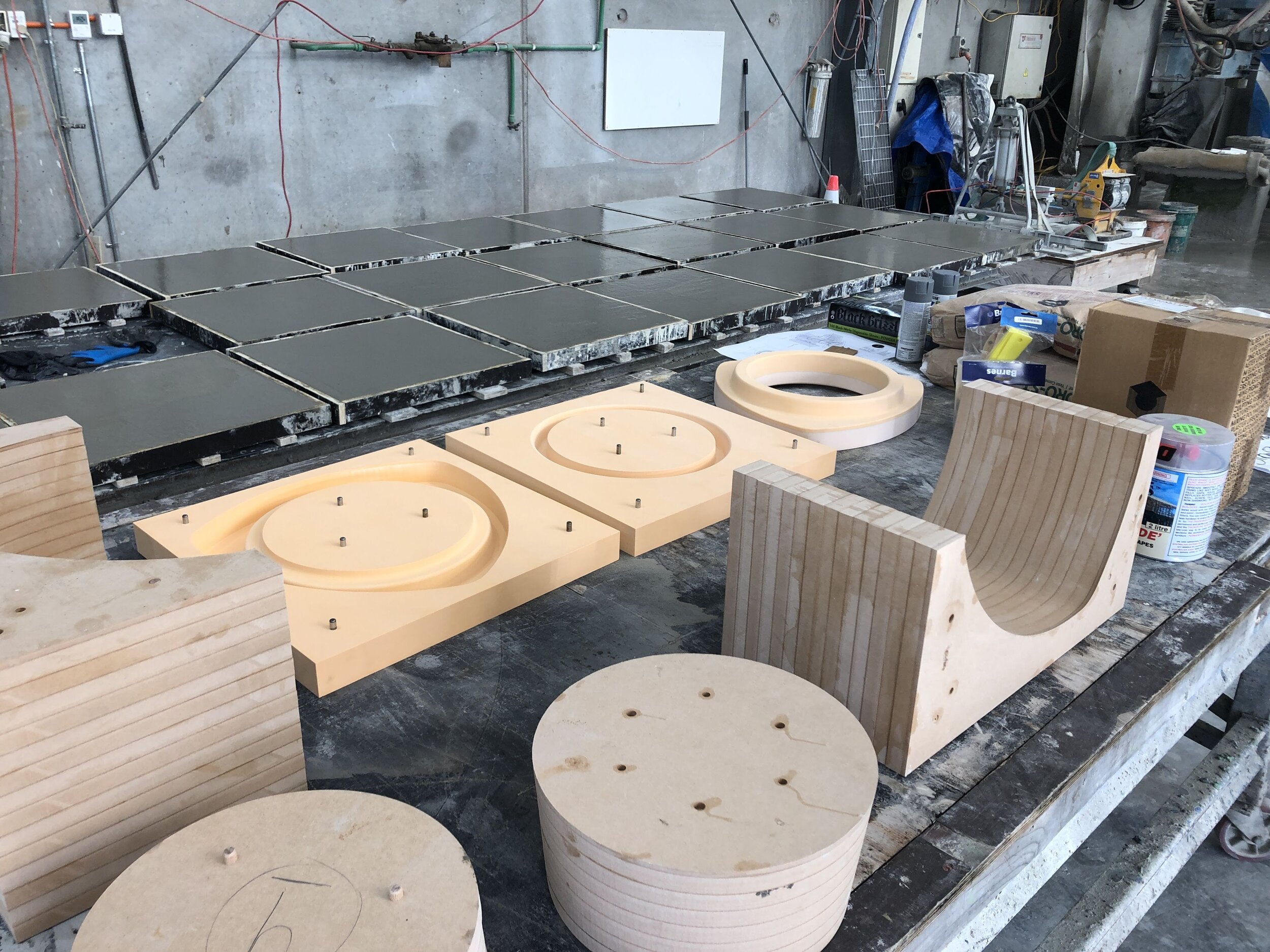

Downloads
Downloads (PDF’s)
FAQs
-
GRC (Glassfibre Reinforced Concrete) is a composite material made of a cement/aggregate slurry reinforced with alkali-resistant (AR) glass fibers. It is a versatile and durable material with various applications in architecture and construction.
-
GRC offers numerous benefits over traditional construction materials:
Lightweight: GRC is significantly lighter than precast concrete, reducing structural loads and transportation costs.
High Strength: Despite being lightweight, GRC has high tensile and flexural strength due to the AR glass fiber reinforcement.
Durability: GRC is resistant to weathering, fire, and impact, making it suitable for various environmental conditions.
Design Flexibility: GRC can be molded into complex shapes and forms, offering architects greater design freedom.
Cost-Effectiveness: GRC's lightweight nature reduces material and labor costs compared to traditional materials.
-
GRC is commonly used for:
Cladding panels: Non-structural exterior panels for aesthetic and weather protection.
Rainscreens: GRC panels can be used to create ventilated facades for improved thermal performance.
Architectural elements: Cornices, moldings, columns, and other decorative features.
Street furniture: Benches, planters, waste receptacles, and other urban amenities.
Drainage channels: Durable and lightweight channels for water management.
-
Liquidstone is committed to high-quality GRC products. Their quality control measures include:
Experienced Personnel: Qualified engineers, drafting personnel, production staff, and quality control managers oversee all stages of production.
Documented Procedures: Stringent procedures for material inspection, shop drawing approval, and production processes.
Testing and Inspection: Regular testing of materials and finished products to ensure compliance with specifications.
Comprehensive Quality Manual: Detailed guidelines for GRC production, ensuring consistent quality standards.
-
Key considerations for designing with GRC include:
Mix Design Compatibility: Ensure compatibility between the face mix and the GRC backing mix to minimize cracking and delamination.
Volume Change: Account for thermal and moisture-induced volume changes in GRC to prevent warping or cracking.
Anchor Design: Properly design and test anchors for handling, transportation, erection, and service loads.
Tolerance Requirements: Establish realistic and achievable tolerances for GRC elements in coordination with other trades.
Finish Selection: Consider the desired aesthetic and performance characteristics when selecting GRC finishes.
-
Yes, Liquidstone offers technical support to assist with GRC design and specification. This may include:
Shop Drawings: Preparation of detailed shop drawings for fabrication and installation.
Sample Panels: Provision of sample panels to demonstrate finishes and quality.
Technical Consultation: Expert advice on GRC design, material selection, and production processes.
-
Regular maintenance helps ensure the long-term performance of GRC elements:
Cleaning: Periodically clean GRC surfaces to remove dirt, stains, and efflorescence.
Sealer Reapplication: Reapply sealers as needed to maintain water repellency and protect against weathering.
Inspection: Inspect GRC elements for any signs of damage or deterioration.
-